在矿石处理的核心环节中,磨矿工序通常占据总能耗的35%-50%。针对某黄金矿山实测数据显示,通过实施系统性节能改造,年度电费支出可降低280万元。本文将深入解析实现节能降耗的关键技术路径。
一、设备选型与参数优化
采用变频驱动技术的球磨机相较传统设备可节能12%-18%。某岩金矿实践表明,将Φ3.2×4.5m球磨机驱动功率从1250kW调整至1100kW,在保证处理量的情况下,单台设备年节电量达86万度。设备匹配需遵循"多碎少磨"原则,当入磨粒度从25mm降至15mm时,单位能耗可降低18-22%。
二、粉碎粒度精准控制体系
引入激光粒度分析仪实时监测系统,使产品合格率提升至92%以上。通过构建粒度-能耗数学模型,当目标粒度从-200目75%调整为80%时,需同步调整磨机转速从临界转速的78%提升至82%,可实现吨矿电耗降低1.8kW·h。
三、研磨介质科学配比方案
采用Φ80:Φ60:Φ40=3:5:2的钢球级配方案,磨矿效率提升19%。某矿厂将介质填充率从32%优化至28%,配合铬钼合金钢球使用,介质消耗量下降40%的同时,处理能力提高15%。定期补充Φ50mm钢球维持级配稳定,可避免效率衰减。
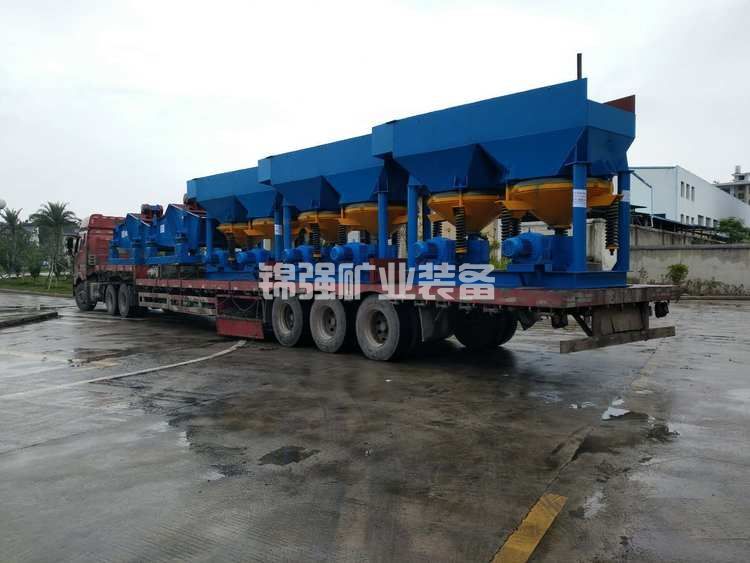
四、智能控制系统集成应用
部署DCS控制系统后,磨矿浓度波动范围从±3%缩小至±0.8%。某智能化改造项目数据显示,通过在线矿浆浓度检测与给料量联动调节,每吨矿石水电消耗分别降低0.3m³和2.1kW·h。设备负载率智能调控模块可使电机效率提升至94%以上。
五、余热回收与能源梯级利用
安装磨机筒体换热装置可回收30%-45%的机械能转化热能。某矿山余热发电系统每年可产出1.2MW清洁电能,相当于节约标准煤960吨。循环水系统采用三级过滤+闭式冷却工艺,使新水补充量减少65%。
某大型岩金矿实施上述综合改造后,磨矿工序单位能耗从23.6kW·h/t降至18.9kW·h/t,设备综合效率(OEE)从68%提升至82%。建议企业建立能耗监测平台,每季度进行能效对标,持续优化生产参数配置,最终实现绿色矿山建设目标。