Tin ore is an important metal ore with high tin content, which can be used to manufacture products such as tin alloys and tinware. However, the mining and processing of tin ore can cause certain environmental pollution, therefore, the research and application of tin ore recovery processes have become increasingly important. This article will introduce the relevant knowledge and operational steps of the tin ore recovery process.
1、 Overview of tin ore recovery process flow
The process of recovering tin ore from mainly includes the following steps: crushing, grinding, flotation, desliming, selection, and tailings treatment. Among them, crushing and grinding are used to refine the tin ore particles for subsequent flotation and desliming treatment. Flotation is the process of separating tin ore from other ores by utilizing the different buoyancy differences between tin ore and other ores in water. Desliming is to remove soil and impurities from the surface of tin ore and improve its purity. Selection is to further improve the purity of tin ore, usually using a combination of gravity separation and flotation. Tailings treatment is to treat wastewater and waste residue generated during the flotation process, reducing their impact on the environment.
2、 Operation steps of tin ore recovery process flow
1. Crushing and grinding
After the transportation of tin ore in the mine, it needs to be crushed and ground. Usually, jaw crushers and ball mills are used for treatment. A crusher crushes large pieces of tin ore into small pieces, while a ball mill grinds small pieces of tin ore into fine powder.
2. Flotation
After crushing and grinding, tin ore needs to undergo flotation treatment. Flotation usually uses air flotation and oil flotation methods. The air flotation method is to spray air into water through a bubble injector, forming bubbles that create buoyancy differences between tin ore and other ores, thereby achieving separation. The oil float method is to spray oil droplets into water through an oil droplet injector, forming oil droplets that create buoyancy differences between tin ore and other ores, thereby achieving separation.
3. Desliming
After flotation treatment, tin ore may have some soil and impurities attached to its surface, requiring desliming treatment. The Hydrocyclone and screen are usually used for desliming. The Hydrocyclone uses the principle of hydrocyclone to separate tin ore and soil. The sieve separator uses a sieve to separate tin ore and soil.
4. Selection
The tin ore after desliming treatment needs to be carefully selected. Selection usually adopts a combination of gravity separation and flotation. Gravity separation is the use of gravity to separate tin ore from other ores. Flotation is the use of bubbles or oil droplets to separate tin ore from other ores.
5. Tailings treatment
After flotation treatment, a certain amount of wastewater and waste residue will be generated, which requires tailings treatment. Tailings treatment usually uses sedimentation and filtration methods. The sedimentation method is to precipitate impurities in wastewater through a sedimentation agent. The filtration method is to filter out impurities in wastewater through a filter.
3、 Conclusion
The tin ore recovery process is a complex process that requires the coordination of various equipment and technologies. In practical applications, it is necessary to choose appropriate process flow and equipment based on the properties and recovery requirements of tin ore. At the same time, it is necessary to pay attention to environmental issues and take effective measures to reduce the impact on the environment.
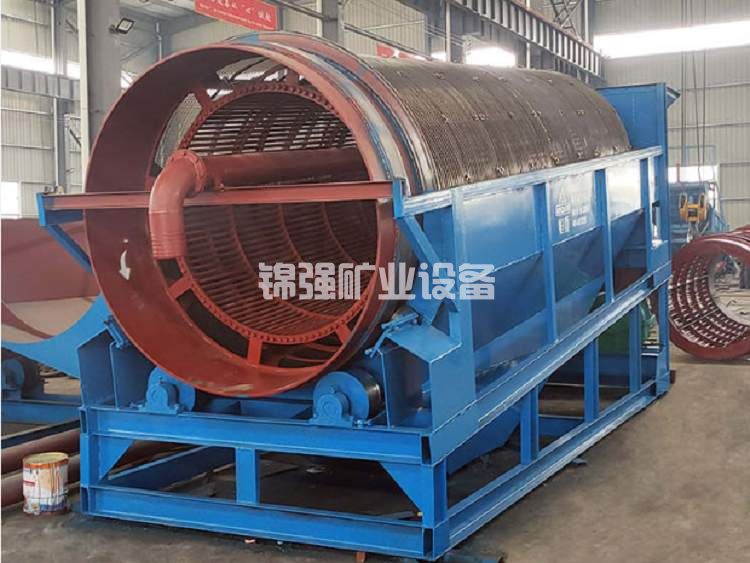