The re selection equipment has a strong sensitivity to the application of standards. There is no complete formula for calculating the production volume of most gravity separation equipment. When clarifying the total number of machine equipment and processing process layout, it is generally recommended to refer to the production and manufacturing of similar iron ores for specific purposes. The production index value varies greatly with ore type, particle size distribution, appearance, coal slurry concentration value, selected grade, specified product quality and processing technology regulations for selected substances.
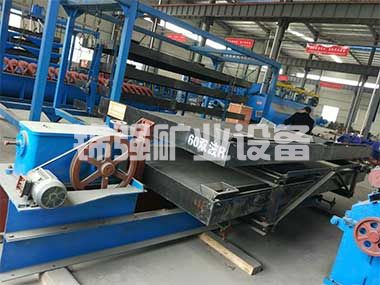
Jig
Jigs are commonly used for mineral processing, tungsten ore, tin, placer gold ore, copper ore, manganese ore, and non gold ore. At present, diaphragm jigs are commonly used in China, which are divided into upward moving, downward moving, and vertical lateral moving types based on the different parts of the diaphragm. When looking down at the jig chamber, it is also divided into rectangular frames, ladder shaped, and circular shapes.
When using jigging in the design scheme, it is important to pay attention to the following difficulties:
(1) The particle size distribution of raw materials and the single dissociation of effective minerals solved by the jig should be fully mastered.
(2) When there is a high content of heavy sand, the difficulty coefficient of jigging will be increased, and the output and titanium concentrate will be severely affected. Heavy sand with a size lower than that of a round hole sieve makes the next screening difficult; Heavy sand exceeding the specifications of the round hole sieve accumulates more and more in the material layer, resulting in insufficient driving force of the replenishment drum and "dead bed". Only when the parking and cleaning sieve produces heavy sand and valuable components in the layer, can the jig work reasonably, resulting in a decrease in machine equipment efficiency and an increase in labor efficiency.
(3) Minimize the particle size distribution of raw materials selected by the jig.
(4) When the total area of the jigging chamber of the jigging machine is large, the four stroke index is small, and the driving force of the supplementary water drum is insufficient and uneven, the material layer cannot be reasonably loosened, resulting in "agglomeration" and inability to perform the jigging function. When designing the plan, the machine equipment manufacturer is required or compensation measures are adopted to get rid of it.
(5) Before the raw materials are fed into the jigger, desliming and proper grading must be applied when there is a large amount of raw sludge or secondary sludge, which is beneficial to improving the actual screening effect. Desliming work should be improved when designing the scheme.
(6) The required working pressure and sufficient water flow rate for the water supply and discharge of the jig should be ensured, especially during dry seasons.
(7) Pay attention to the selection and clarification of standards such as the Degree distribution and relative density of the jig human bed stone particles.
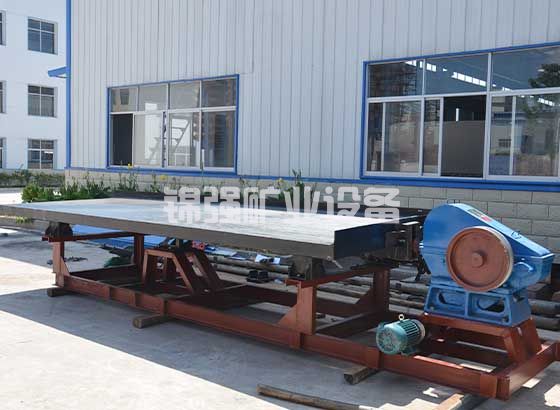
Rocking bed
Shaker is a gravity separation equipment for selecting fine sand raw materials, which can obtain high-quality titanium concentrate, waste tailings storage, and mineral resources in one go. The shaking table can be divided into coarse sand (2-0.074mm) shaking table, fine sand (0.5-0.074mm) shaking table, and mineral mud (0.074-0.02mm) shaking table, and their differences depend on the aspect ratio (or deep depth) of the bed strips (or grooves) on the bed surface and the cross-sectional shape. According to the different requirements of the bed, it can be divided into tin shaker, CC-2 shaker, torsion spring shaker, and 6-S shaker.
The total area output of shaking table enterprises is relatively small, accounting for a large proportion of the total area. Some reprocessing plants use tin six layer mineral mud shaking tables, which can acquire 74-19 μ The working capacity of the heavy ore material with the particle size distribution of m can be twice larger than that of the same size and model of the bed on one side. However, attention must be paid to the design scheme. Even if the feed particle size distribution is the same, the four stroke and stroke times are similar. For different types and grades of raw materials, the working capacity of the table is very different.
chute
(1) Spiral concentrator and spiral chute
The characteristics of these two types of machinery and equipment are simple construction, reliable operation, small footprint, and high output of the enterprise. Spiral concentrator is suitable for screening particle size distribution of 2~0.1mm; The spiral chute section of the spiral chute is cubic meter hyperbolic type, and the chute bottom inclination angle is smaller than the spiral cleaner chute bottom inclination angle, slightly wide and gentle, suitable for screening 0.6~0.05mm thin raw materials. The distance to diameter ratio is generally taken as 0.5~0.6. Moderate expansion of the tooth pitch is beneficial for screening fine sand raw materials, while it is beneficial for coarse-grained raw materials. The number of turns in the spiral type is 4-6. The specifications and models are indicated by the spiral diameter, and the specifications and models of the spiral concentrator include ф 600 ф 800 ф 1000 ф 200mm, spiral chute specifications and models available ф 600 ф 900 ф 1200, the spiral chute still needs to obtain the pitch value.
When using a spiral concentrator and spiral chute in the design scheme, the main parameters such as diameter, cross-sectional shape of the chute, tooth pitch, and factors are effectively defined. When the diameter exceeds 100mm, it is generally divided into 2-1mm coarse grade raw materials, and when the diameter is less than 100mm, it is generally divided into 1-0.05mm raw materials.
In practical life, there are spiral chutes, LL type spiral chutes, and acid pickling chutes made of fiberglass anti-corrosion chemical fibers, which improve the production and manufacturing of epoxy resin. They have small quality, high compressive strength, precise appearance, waterproof, rust proof, and anti-corrosion treatment, and have specifications and models ф 600 ф 900 ф 1200, tooth pitch 720 Mm; The TT-12 rotary spiral chute is equipped with a grooved wedge shaped vulcanized rubber lining, and its screening index value is better than that of the spiral chute and spiral concentrator. The specifications and models include ф 600min360Mm ф 600min338mm
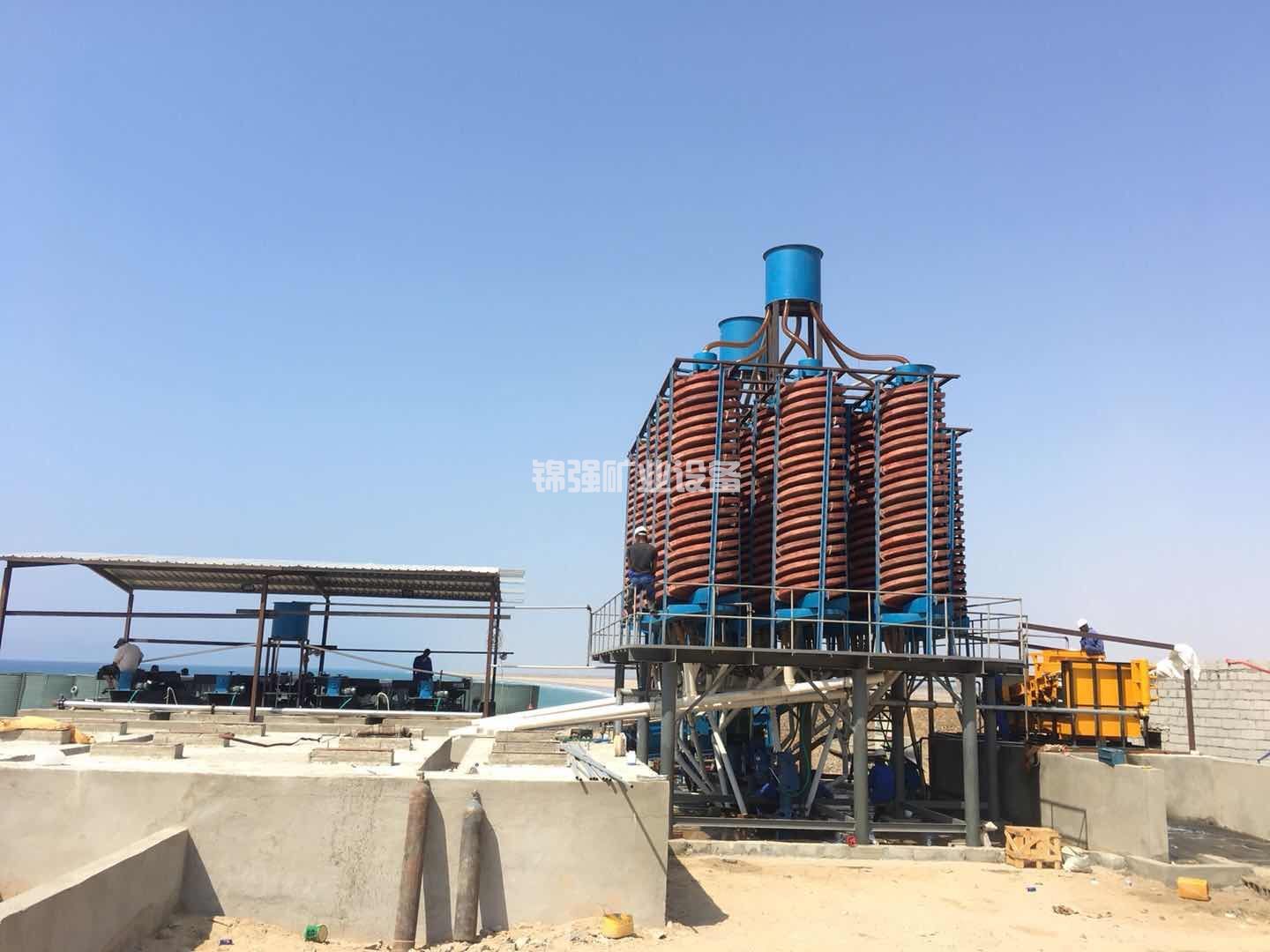
(2) Drive belt chute
The transmission belt chute is a mineral mud optimization machine equipment developed in China. Coal slurry and cleaning water are evenly distributed onto the surface of the belt, and the flow layer needs to be maintained thin and stable. Heavy minerals accumulate on the surface of the belt and unload from the first round with the rotation of the drive belt. Light minerals flow in with the ore, and the lower limit of particle size distribution is 19~10 μ m. Used for the production of tungsten tin ore slurry, the production capacity is low, and the output of a 100min 2500m transmission belt chute is only 1t/h.
(3) Diffuse flow transmission belt chute
The bulk flow transmission belt chute uses the basic principle of cutting flow film to promote the looseness and gradation of ore particles, and reasonably purchases the particle size distribution of 0.1~0.01mm. At the same time, different products with different output rates gather higher production than the transmission belt chute, which is an excellent mineral mud gravity separation equipment. This machine and equipment are mostly used to solve the problem of air oxidation of tin ore slime in Yunxi. The machine and equipment include XZH12002750, with a daily working capacity of 3-4 tons.
Cone concentrator
The cone concentrator is improved by a fan shaped chute, which removes the outer wall effect of the fan shaped chute. The basic module of the cone concentrator is an inverted cone made of fiberglass anti-corrosion, which is tilted from a circle to the management center. Assembling into a single sided cone, it can also be assembled into a two-layer cone. The latter type is a two-layer cone selection surface, which increases the output of the machine equipment. The two-layer cone is used for rough selection and the single-sided cone is used for optimization. According to the characteristics of iron ore and the different requirements for product quality, the accumulation of two-layer cones and single-sided cones becomes a two-stage sorting generator set. Rough selection, optimization, and scanning can be continuously carried out on the same generator set.
Centrifugal concentrator
The particle size distribution of the selected raw materials suitable for the centrifugal concentrator is -0.074mm, and the reasonable purchase particle size distribution is 0.074~0.010Mm. This vertical centrifugal concentrator has two types of cylindrical screens, namely single cylindrical screen and double cylindrical screen. The smoothness of the cylindrical screen can be divided into single smoothness and double taper. At present, tungsten, tin and Hematite are all selected in China, and there are two specifications and models, namely ф eight hundred ф 1600900Mm. This machine and equipment cannot continue to operate due to high water consumption, high pressure, and uniform feeding.