The selection principle of spiral chutes.
The spiral chute is formed by connecting 4-6 spiral chutes. Made of rubber tires or cast iron or ceramic grooves. When a certain concentration of slurry enters the upper part of the spiral separator, under the action of gravity and centrifugal force, the slurry rotates downward along the spiral groove. Larger mineral particles first sink into the bottom of the trough, while smaller mineral particles flow in the upper layer of the mineral particles. The high density mineral particles that sink into the bottom of the trough, due to the small impact force of water flow, high friction force, low velocity along the trough, and low centrifugal force, are close to the inner edge of the trough during their movement. The small specific gravity mineral particles moving in the upper layer of the slurry are close to the outer edge of the groove due to the high water flow velocity in the upper layer, the high flow velocity along the groove, and the high centrifugal force. This allows for the interception of mineral particles with different specific gravity at different positions of the helix, achieving the purpose of selection.
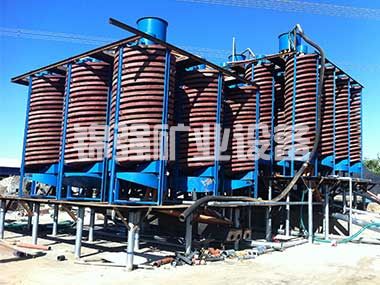
The selection principle of spiral chutes.
There are many operational factors for spiral chutes, including feed volume, feed concentration, structural parameters of flushing water equipment, process operating parameters, spiral groove diameter, pitch, and number of spiral groove turns.
One is the amount of ore provided.
The ore feeding amount is related to the diameter, spiral angle, cross-sectional shape of the spiral chute, and raw ore properties of the spiral concentrator. As the diameter and angle of the helix increase, the finer the particle size of the raw ore and heavy product, the higher the mud content, and the lower the productivity.
The second is the feed concentration.
The feed concentration not only affects the grading particle size, but also affects the processing capacity under the particle size. At a certain critical concentration, when the precipitation reaches a large value, the corresponding weight concentration is called the critical concentration. At critical concentrations, the processing capacity of spiral chutes is greater. The critical concentration varies with the ore density and mud content, and is related to the specified grading particle size. As the density of the ore increases, the critical concentration by weight increases. However, as the mud content increases, the critical concentration will decrease. The feed concentration during beneficiation should be lower than that during rough beneficiation, and the feed concentration of the concentrator is generally 11-14%.
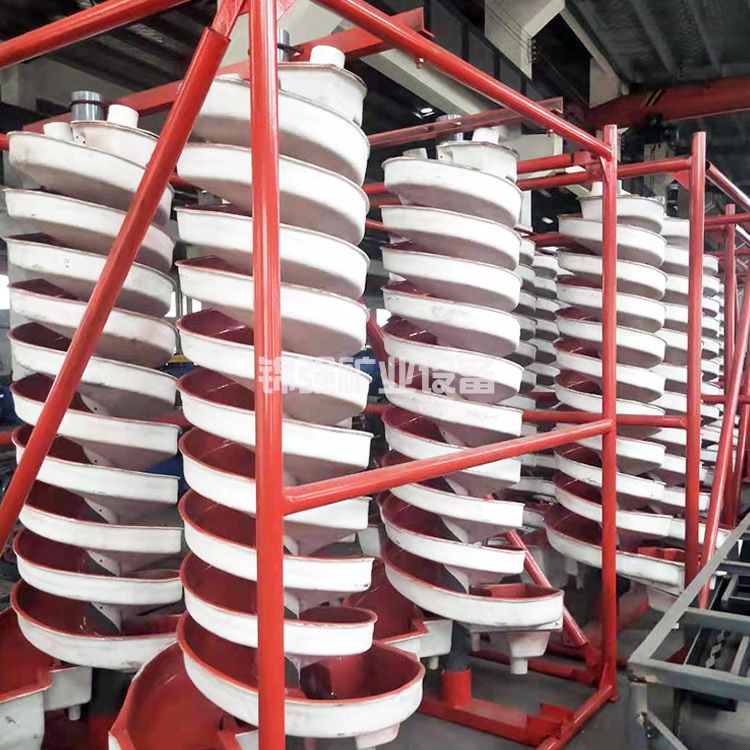
The impact of grading particle size on the critical concentration is the same as the ton content, that is, as the grading particle size decreases, the critical concentration decreases. If the feed concentration is fixed in actual production, the overflow concentration will remain unchanged, and the particle size of the graded product will also remain unchanged. Therefore, controlling the feed concentration of the spiral equipment has become an effective means of controlling the overflow concentration. To form a closed spiral groove with the mill, a fixed amount of water must be added to the constant pressure tank before the grinding product enters the equipment to ensure that the feed concentration is at an appropriate value. The equipment itself can produce fine-grained products. As the amount of recycled sand increases, the amount of ore entering the chute increases, resulting in an increase in feed concentration and a coarsening of overflow particle size. Ultimately, this is because the grading particle size depends on the fineness of the mill. The overflow product of the spiral chute equipment is the final product of grinding.
3、 Washing water volume.
The amount of washing water should also be appropriately controlled, as its main function can improve the quality of heavy products.
4、 Equipment structural parameters.
The structural parameters of the spiral chute equipment include diameter, cross-sectional shape, pitch, length and number of turns of the spiral chute. The diameter of the spiral chute is the specification mark of the equipment, and the processing capacity of the chute is directly proportional to the square of the diameter. The lower limit of particle size recovery increases with the increase of the diameter. When conditions permit, large diameter spiral grooves should be used to handle thicker materials. The cross-sectional shape of the spiral chute is related to the particle size of the treated material. For raw materials less than 2mm, the ratio of the long to short axis is 2:1, and the long axis is horizontal, with half of it equal to one-third of the spiral diameter. The size of a spiral chute is usually represented by the ratio of its diameter to the diameter of the spiral, which is called the distance to diameter ratio. The value is around 0.73, and the selection effect is better. The length and number of turns of the spiral chute determine the running distance of the material. Easy to choose ores only require 3-4 laps, while difficult to choose ores require 5-6 laps.

5、 Process operation parameters.
Operating parameters mainly refer to adjustable parameters in production such as ore volume and ore concentration. The variation of feed weight concentration between 10% -35% has little impact on the sorting index, and high or low concentration will reduce the beneficiation recovery rate. The impact of changing the mine volume on sorting indicators is roughly the same as changing the mine concentration. Generally speaking, the feed concentration for rough selection is 30% -40%, and for selection is 40% -60%. The feed volume and concentration during the production process fluctuate within an appropriate error range of 5%.
6. The diameter, pitch, and quantity of spiral chutes.
Increasing the processing capacity of the spiral diameter can greatly increase, but the strength recovery offline will also increase. The main control factors in operation are the feed volume and feed concentration. When selecting coarse particle size, the ore volume can be larger and the fine particle size can be smaller. The feed concentration of rough selection operation is lower than that of selection operation. For example, when selecting Hematite, the feeding concentration of rough selection is 30% -40%, while it is better to control it at 40% -60% when cleaning. In practical operation, fluctuations in feed volume and feed concentration within 5% have little impact on sorting indicators.